Digester For Paper Bag Making Machine
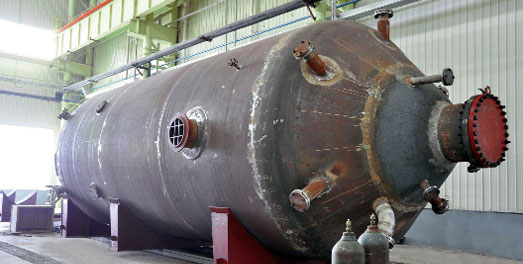
Digester series are our leading products. We can manufacture various specifications of digester for paper pulp process, including 50m3, 75m3, 110m3, 135m3, 175m3, 225m3, 250m3 and 400M3 digesters used in paper pulp digester workshop. The maximum size of the paper pulp digester is 5.8m in diameter and 400m3 in volume. According to different production technologies of alkaline pulping and acid pulping, digester series can be made of different raw materials for example, carbon steel structure, composite steel structure or dual-phase stainless steel. Digester for paper bag making machine series are mainly used to chemical pulp and dissolved fiber steaming section. Our paper pulp digester can compare favorably with similar productions made by GLV or other famous international companies of chemical pulp production line equipments, so our paper pulp digester are widely used in China.
Conventional Digester Room And Subsidiaries
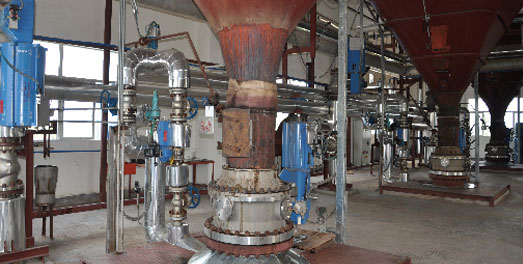
Digester used in conventional paper pulp digester room is mainly applied to pulp cooking through the use of raw materials such as wood or bamboo with less than 15% moisture content, 2%-3% ash content, 50%-55% cellulose content, 22%-25% lignin content and less than 3% Si content. After being cut into the slices (25mm-30mm), raw materials will be sent to the digester with full of cooking liquor and steam through a conveyor belt. The cooking process will take 5.5-6 hours at the temperature of 160℃-175℃ to make. The time span depends on the pulping demand (Pulp yield and hardness). The digester for paper pulp process occurs mainly in the effective indirect heating area where tubular heater works. Liquid out from the center flows through circular tube whilst is heated and transmitted from up to down, which shall be circularly carried out for about 8-12 times an hour. Meantime the steam from the vent at the bottom will help do auxiliary heating. During the cooking process gas is expelled out form the vent at the top to reduce the fake pressure phenomenon caused by the air in the inner digester, which is conducive to keep the uniform of pulp cooking and improve the pulp quality. After the cooking process, through the blow valve the pulp under pressure will be out of the digester and enter the flat discharge pan where it will be stored temporarily.
Displacement Digester And Subsidiaries
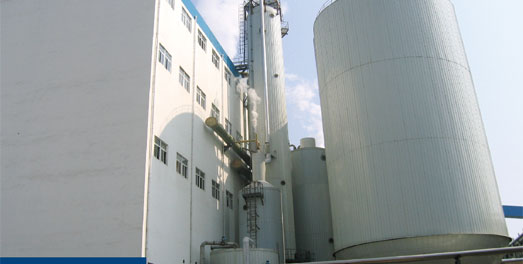
Displacement cooking is that used cooking liquor is displaced by cooking liquor or washing water using the principles of displacement cycle and diffusion washing of black liquor in the batch digester. Both used cooking liquor and heat are displaced, and then cold spraying is fulfilled. Displacement cooking can make full use of the black liquor repeatedly, extract lignin from the cooking system in delignification phase and dissolve hemi-cellulose. During the supplementary delignification phase, cooking liquor can be refilled. By the principles, initial heat and chemicals can be recycled. The cooking can keep continuous balance during the whole cooking process, which can help to improve pulp quality and production efficiency.
Advantages
Displacement cooking technology is the most advanced batch cooking technology in the world nowadays. Compared with conventional cooking, it has the following advantages:
- Per-ton pulp of steam consumption is reduced greatly to 0.6-0.8t (Conventional consumption is 2.0-2.5t).
- It can achieve low Kappa number, high strength and high yield pulp through deep delignification.
- Pulp has gotten better bleaching. Its low Kappa number and high strength are conducive to oxygen delignification, reduction of consumption of chemicals for bleaching and reduction of pollution.
- Digester for paper pulp process is controlled by microcomputer, which reduces manual operation as much as possible and keeps the system reliable and stable.
Super Batch Cooking Production Line
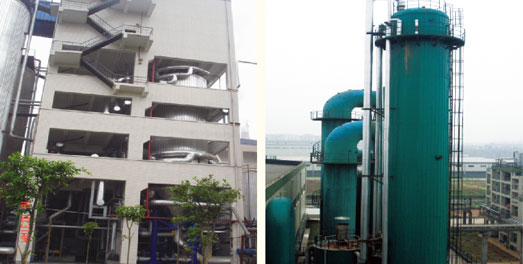
According to different raw materials, the technology can be also applied to produce dissolving pulp.
In 2007,based on the characteristics of conventional cooking, our company has developed a 300,000t of annual output of super batch cooking production line that adopts an efficient pulping technology with making use of new energy on the basis of conventional cooking technology, which can save about 60% of cooking steam consumption that is roughly equivalent to the reduction of 10,000t annual coal consumption (Standard coal as measurement unit).Meanwhile, we can reduce by about 15% of SO2 emission (sulfur dioxide) and soot aggregates from the alkali recovery boiler, achieving zero emission wastewater and reducing the emission of bleaching wastewater.
Advantages
- Compared to conventional cooking steam consumption, our paper pulp digester equipments can achieve great reduction of that. Our super batch cooking technology can reduce to 0.6-0.8ton of steam consumption from 2-2.5ton for producing1ton pulp.
- Oxygen delignification; Low Kappa value; High strength of paper.
- Pulp has excellent bleaching properties for the reasons of low Kappa value, high strength, oxygen delignification and good production conditions. Meanwhile, relevant chemical consumption drops down, which not only reduces environmental pollution, but also lowers paper cost.
- The whole production digester for paper pulp process is fully under automatic control, and then the system reliability is greatly improved, and therefore pulp quality is stable and reliable.
Continuous Cooking System
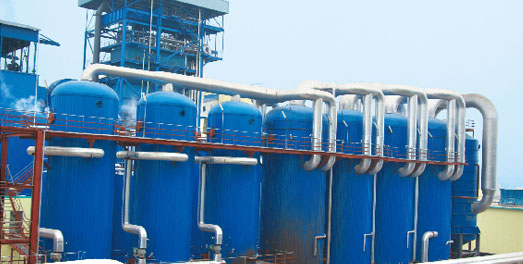
Continuous cooking digester for paper pulp process refers to the whole continuous process from feeding to discharging, and digester for paper pulp process is mainly used to alkaline pulping and nitrite cooking, prehydrolysis sulfate and sulfate cooking. Nowadays it’s developed and applied to various raw materials of pulping including wood chips, non-wood fiber of raw materials with loosing structures and easy penetration such as bagasse, reeds, wheat straw, rice straw, etc.
Advantages
- Lower energy consumption: lower steam and electricity consumption, without peak load.
- Higher paper pulp production, smaller floor space.
- Low consumption of per unit of chemicals.
- More homogenized cooking and less rejects.
- Easier automatic operation and lower labor intensity.