Green Liquor Semi-chemical Pulp
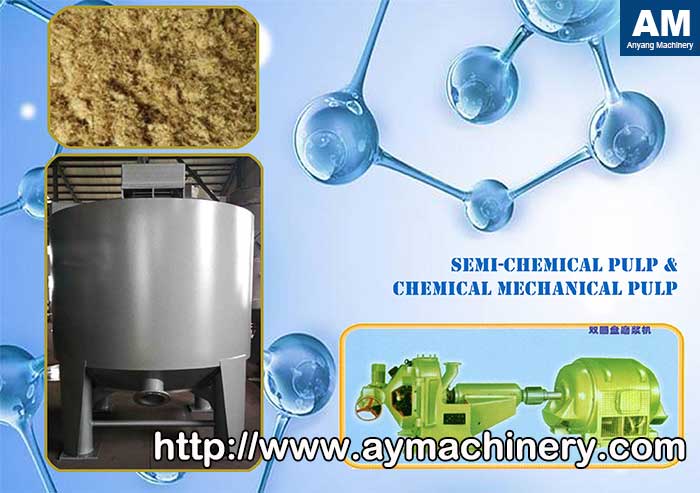
In recent years, it is the development result that semi-chemical pulp is produced by use of green liquor of ordinary sulfate with the sulfidity of 25% or green liquor with high sulfidity (50%) after being removed part of sodium carbonate. It is the pre-steaming production method. Specifically, Wood chips shall be performed pressure impregnation for a short time at the temperature range of 75℃-80℃, and then had a gas phase cooking at 150℃-160℃ for 15-20minutes. This is more convenient in a continuous digester. In foreign countries, people take use of hardwood as raw material. When green liquor of ordinary sulfate is used for pulp making, the pulp with the yield of 72%-76% can be obtained after being kept at the temperature for 20 minutes. Compared with neutral sulfite semi-chemical pulp, this green liquor semi-chemical pulp has a lower chemical consumption of only 7.90% Na20 (Just for dry wood). At a certain yield, the properties of the corrugated board pulp obtained (Such as ring crush strength) are very similar. The method is simple in chemical recovery and low in investment costs. Especially it is more convenient to be attached to the sulfate plant production. Green liquor semi-chemical pulp is darker in color, so it can only be used at the plants in less demand on whiteness for producing liner cardboard or corrugated cardboard.
Non-sulfur Semi-chemical Pulp
It is a semi-chemical pulping method that has emerged in recent years to prevent air pollution. The chemical solution is sodium carbonate or a mixture of sodium carbonate and caustic soda. By the cooking with 6% of Na2CO3 (For wood) at 170℃ for 30 minutes, people can obtain 85% yield of birch pulp and 88% beech pulp. Compared with the neutral sodium sulfite semi-chemical method, this method is similar in terms of yield and strength. Using it for making corrugated cardboard can save 5%-10% of production cost compared with the same quality of neutral sulfite semi-chemical pulp. This method can be operated in conjunction with the sulfate plant or separately.
Mechanical Processing of Semi-chemical Pulp
After being cooked, raw material does not mean that the semi-chemical pulp has been produced. The mild chemical reaction only brings about a certain degree of fiber tissue relaxation. To meet the requirements of semi-chemical pulp for papermaking, people must perform mechanical processing. The roles of mechanical processing include: first, soften cooked raw material by the use of heat generated by mutual friction to further weaken the fiber connection; second, split the fiber connection to dissociate into a single fiber; third, the fine fibrillation of a single fiber, that is, make the complete fiber part into a large surface area of small fibers to enhance the binding capacity between the fibers. The degree of fiber dissociation and fibrillation depends largely on the input function and the pulp throughput, which can be controlled depending on the applied purposes. These effects of mechanical processing can be achieved in one or more stages. These functions depend on the type of raw material, size, cooking method and degree and the papermaking requirements.
Mechanical processing equipment is mainly disc refiner or disc mill. The double disc refiner is more popularly used in defibrillation process. It is equipped with two opposite-direction rotation discs with the diameter from 600mm to 1000mm, the speed of 600-1800rev/min and the maximum power of 1100kilowatts. Various types of disc refiners are sensitive to metallic iron, so they must be electromagnetically removed prior to dissociating the fibers. In order to protect the disc refiner, the magnetic separator is equipped on the belt conveyor. Even under normal operation, the gear disc is easy to be worn. In order to facilitate the replacement, it can be divided into several sections according to the entire circular surface. The service life of a set of gear disc can reach 500-2000hours, which is related to the operating conditions and manufacturing materials. Gear disc material can be made of chilled cast iron, ordinary carbon steel, stainless steel, nickel steel and others. In China, it is made of chilled cast iron. We have accumulated some experience, and the service life continues to grow. We have owned a variety of gear types that are related to the requirements of refining quality.
Refining conditions can be adjusted and controlled according to production needs. The most important several refining variables are: rotation speed, distance between discs, load, temperature and concentration. These variables are mutually constrained and influenced each other. High rotation speed (900-1800rpm) and high concentration (8%-15%) are required for fiber dissociation, but low rotation speed (450-900rpm) and medium concentration (5%-8%) are required for improving the pulp quality. Taking use of disc refiner as half pulp at the first section of coarse grinding alkaline cooking, it tends to result in phenomenon of stickiness, washing, dehydrate difficulties, clogging wear control and big loss and so on. In some plants the hydraulic repulper is used instead of disc refiner, achieving good results.
Anyang Machinery Co., Ltd. (AM) is affiliated to China National United Equipment Group Corp. Now the wholly state-owned key mainstay enterprise of China National Building Materials Group Corporation (CNBM) belongs to China National United Equipment Group Corp. under China’s State-owned Assets Supervision and Administration Commission of the State Council. AM has its own the R&D center of product design and provincial technical center. AM’s leading products include large chemical vessel, tower, reaction kettle, heat exchanger, a complete set of pulp production line, batch cooking equipment, a complete set of pulping equipments for large chemical pulp production line, APMP poplar CMP equipment, multi-disc vacuum filter and complete sets of equipments for hollow brick, fly ash brick and aerated concrete block of production line. Meanwhile, AM is also working hard in a large number of the design, manufacture and installation of pressure vessel and machinery equipments referring to the industries of metallurgy, building materials, power and environmental protection, etc. in recent years.