What is Paper Pulp Digester?
Paper pulp digester is main equipment used to make chemical pulp. It is to cook raw materials of papermaking (For example, wood, grass, bamboo, etc.) to produce the pulp mainly containing the cellulose by chemical interaction with the cooking liquor.
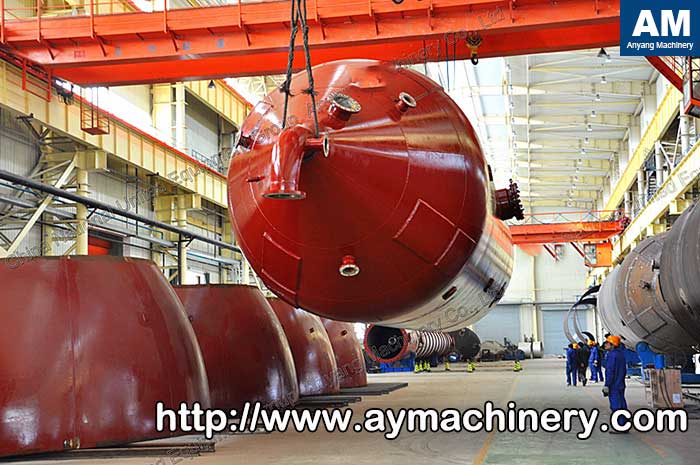
What Kind of Role Does Paper Pulp Digester Play in Paper Pulp Processing?
Main Steps of Paper Pulp Processing
Paper pulp processing refers to the production activity of paper pulp by mechanical or chemical processing method. It can be generally divided into the following main steps:
Wood storage → Wood sawing → Debarking and Knotting→ Wood cutting for chips→Cooking→Washing→Screening and Purifying→Unbleached pulp (or→ Bleaching→Bleached pulp) →Soaking and Refining
Paper mill digester is used for the cooking process. The cooking process is an important step in the pulp processing process. It is a complex chemical process. It is to send the plant fiber raw material after the mechanical pretreatment into the digester with chemical cooking liquor under high temperature and pressure for further treatment. The lignin and other impurities will be dissolved and removed. Finally, the chemical pulp is obtained. The purpose of the cooking process is to remove the lignin in the fiber raw material, retain cellulose and hemicellulose and dissociate the fibers into the required pulp by using chemical agents according to the needs of different types of pulps.
Main Factors Affecting the Cooking Quality
Taking alkaline pulping as an example, main factors affecting the cooking quality in the alkaline pulping process are as follows:
Variety, specification and quality of plant fiber raw material
A. Variety
The grass is easy to be cooked, but the pulp yield is low. Wood is hard to be cooked, but the strength is high. Bamboo is suitable for the sulfate cooking process.
B. Specification and quality
Wood chip is 3-5mm in thickness. Smaller or thinner chips cannot meet the cooking requirement. The bark content must be controlled.
Alkali consumption, liquor concentration and liquor ratio
Alkali consumption depends mainly on chemical composition, distribution and structure of raw material and the quality requirements of the finished pulp. Besides, the specifications and quality of the raw material chip and the cooking temperature and time are also crucial.
When alkali consumption is certainly fixed, liquor concentration and liquor ratio will meet the following situations: as the ratio is higher, the concentration is lower; as the ratio is lower, the concentration is higher. When the concentration is higher, it will not only damage cellulose and hemicellulose but also get uncooked in local part easily although the cooking speed can be improved and the pulp yield is increased. Therefore, in general, following factors must be also considered in the selection: a. cooking method; b. digester; c. variety of raw material.
Sulfide
When alkali consumption is certainly fixed and other conditions are the same, increasing sulfide can shorten the cooking time, reduce the lignin content and ensure a higher yield. But when the alkali consumption is too high (More than 40%), the result will be converse due to the decline of effective alkali content. When being cooked by the sulfate method, softwood shall be controlled at 25%-35%, hardwood 15%-25%, bamboo 20% -30% and grass 10%-20%.
Cooking time and temperature
Cooking time includes the heating time and the holding time. Both times affect and restrict each other. Cooking temperature refers to the highest cooking temperature. In the cooking chemical reaction, as the temperature increases by 10 ℃, the chemical reaction rate can be doubled. However, the higher the temperature gets, the lower the pulp yield and pulp lignin content will be. The maximum temperature of cooking wood is generally 160℃-180℃, reed and bamboo 160℃-170℃, rice and wheat straw 150℃-160℃.
Digester classification
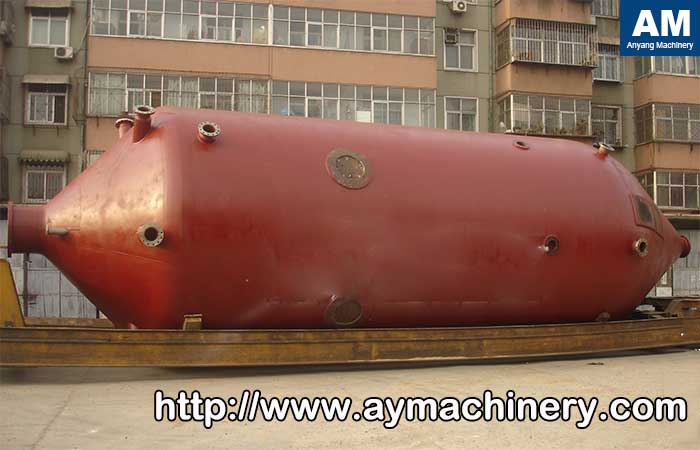
Digester can be divided into batch type and continuous type:
-
The batch digester can be also divided into vertical type or horizontal type of cylindrical and spherical pressure vessels. Both are heated with steam.
The vertical digester is commonly known as bog pot. It has a larger capacity. It is a fixed device and usually attached to liquor circulation equipment. The spherical digester is commonly known a steam ball. It has a smaller capacity and is a rotary device. - Continuous digester includes tube type and vertical type. It is equipped with the automatic metering device and the control equipment. It is a new type of digester and suitable for caustic soda method, sulfate method or semi-chemical method to produce wood pulp, straw pulp and so on.
Industry Prospects
The traditional batch cooking digester has the advantages of more flexible production, better mechanical reliability, and lower investment. The continuous cooking digester has the advantages of lower energy consumption, more stable pulp quality and less pollution load. Especially, the deep delignification theory makes continuous cooking technology is more perfect. In 1981, Beloit Company began to develop the technology of rapid replacement heating (RDH) system for batch cooking. The technology makes good use of original batch cooking equipment. The principle is to use thermal replacement method to achieve cold spraying and heat recovery, which cannot only improve the strength of the pulp but also reduce energy consumption.
Displacement Digester System (DDS) is a new pulping technology developed by CPL Company based on original RDH digester system from Beloit Company. DDS inherits the advantages of RDH and improves several technical aspects of the RDH process. The system has a strong and stable tank area, which is achieved by adding special separators in hot and warm black liquor tanks. In addition, the advanced control technologies such as MPC, multivariable control, etc. reduce the impacts on the cooking operations.
For a pulp mill, the cooking process is the heart of the entire mill. It is crucial for the viability and competitiveness. In the paper manufacturing process, DDS cooking system has become the preferred equipment for modern papermaking mill. Therefore, the paper pulp digester matched with DDS cooking system is the focus of the industry.
CNBM Leadership in the Pulp Industry
Paper pulp digester is one of the main products of CNBM. We can produce the digesters with a variety of volumes including 50m3, 75m3, 110m3, 135m3, 175m3, 225m3, 250m3 and 400m3. We can also produce a series of digesters used in the cooking workshop. The maximum diameter is 5.8m, and the maximum capacity is 400m3. In view of different processes of alkaline pulp and acidic pulp, the digesters are made of carbon steel, composite steel or duplex stainless steel. The digesters are mainly used for chemical pulp and dissolved fiber steaming operation. Our digesters can be compatible with GLV's products and the products from other well-known international manufacturers. So our products have been widely used at home and abroad.