Different Paper Pulp Raw Materials Need Different Pulp Manufacturing Methods
As we known, in the pulp manufacturing process, there are many kinds of raw materials for paper pulp, such as wood, bamboo and waste paper. Generally, different raw materials must be adopted in different methods for pulp making.
Pulp Manufacturing Methods
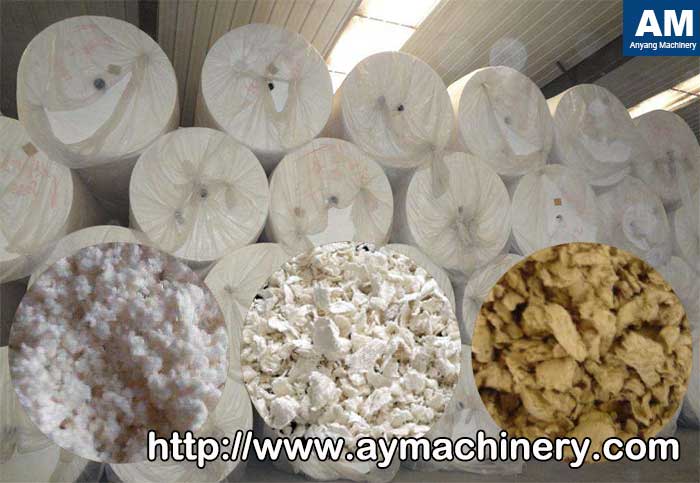
Pulp manufacturing methods include: mechanical grinding method, chemical treatment method and combination method of chemical treatment with mechanical grinding. During the process, plant raw materials shall be separated into the morphology of single fiber to meet the requirements of cleanness in use.
Pulping methods are basically divided into three categories:
Mechanical pulp manufacturing methods
It is the method mainly based on mechanical grinding (mechanical dissociation) for fiber separation. Pulping yield, that is, the weight percentage of paper pulp obtained from a certain amount of raw material, Mechanical pulp manufacturing has the highest yield in all the methods. About wood raw material, it can reach up 95%.
Chemical pulp manufacturing methods
It is the method of obtaining pulp by use of chemical agents to cook plant raw materials for paper pulp. Its pulping yield is about 40% to 50%. The high yield of chemical pulp can reach up 65%.
Combination pulping pulp manufacturing methods
It is to use chemical agents to make some certain of pretreatment on raw material and then adopt mechanical grinding method to obtain pulp.
According to chemical pretreatment, its pulping yield is between 65%-94%. It is popular to call a pulping method with a yield of 65%-84% as semi-chemical pulping method but call the pulp manufacturing method with a yield of 85%-94% as chemical mechanical pulping. But both are made by chemical mechanical pulp manufacturing methods.
Pulps obtained by various pulp manufacturing methods must be treated through appropriate washing, screening, impurity removal or further bleaching and refining to improve the quality and meet the requirements for producing different types of paper. Waste paper fiber can also be properly treated and re-made into paper pulp. But its process principle and production flow are different from those of the above pulp methods.
The Category of Pulp Manufacturing Methods
- 1. According to different manufacturing methods, it is divided into chemical pulp (Including caustic soda pulp, sulfate pulp, sulfite pulp, etc.), mechanical pulp (Including SGW pulp, RMP pulp, TMP pulp, etc.) and Chemical mechanical pulp.
- 2. According to different raw materials for paper pulp, it is divided into wood pulp, straw pulp, bamboo pulp, cotton pulp, waste paper pulp.
- 3. According to different processing grades, it is divided into unbleached pulp, half-bleached pulp, bleached pulp, refined pulp, etc.
- 4. According to different pulp yields, it is divided into chemical pulp (40%-50%), high yield of chemical pulp (50%-65%), semi-chemical pulp (65%-84%), chemical mechanical pulp (85%-94%), mechanical pulp (94%-98%).
- 5. According to different application purposes, it is divided into self-use pulp and commodity pulp. For a specific category, it is often named by several different classification methods, for example, bleached sulfate softwood pulp, unbleached sulfite reed pulp, poplar wood pulp and others, so that the user can generally understand the properties and uses of pulp from their names.
Of all categories of pulps, chemical pulp still occupies the largest proportion. In 1987, chemical pulp manufacturing production reached 111,350,000tons in the world, accounting for 71% of the total pulp production (155,860,000tons) and mechanical pulp accounts for 21%. Chemical mechanical pulp grew rapidly in recent years although it is used relatively late. Due to continuous improvement of pulp manufacturing recycling rate of waste paper and relative increases in the amount of fillers and coatings used in paper, pulp consumption reduces. So the growth rate of pulp is generally lower than that of paper and cardboard.
Quality Evaluation and Selection of Pulp Manufacturing Methods
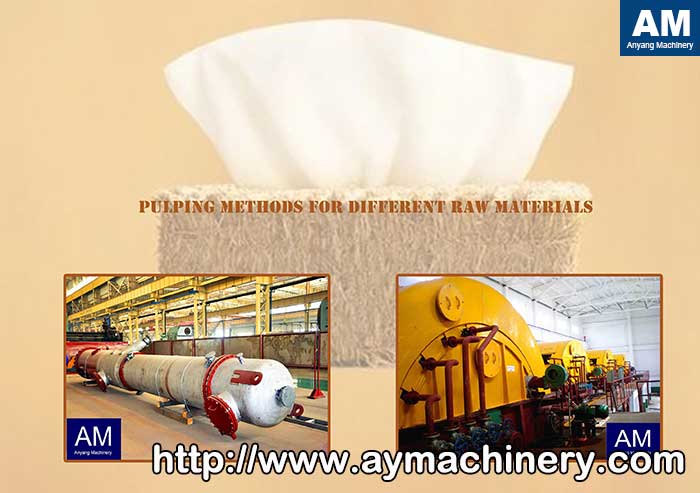
Pulp manufacturing quality mainly depends on its fiber morphology and fiber purity. The natures of these two aspects are mainly determined by raw materials, manufacturing method and processing grade of paper pulp.
In terms of fiber morphology, it is mainly the average length of the fiber. It is well known that as the average fiber is longer, the ratio of the thickness of cell wall to the cell diameter is smaller.
The pulp with no cells or few non-fibrous cells and fiber bundles has good characteristics of bonding strength, dehydration and papermaking performance, which can produce stronger paper and belong to higher grade pulp, such as spruce softwood pulp, cotton & linen pulp, etc.
In terms of fiber purity, good quality pulp has high cellulose content and low content of other components. The pulp has high durability, strong binding performance, high whiteness and good electrical insulation and other excellent performances.
Different uses and grades of paper have different quality requirements. It is unnecessary to choose the pulp with best fiber morphology and highest fiber purity at any time. General principle is to choose to both meet quality requirements of production and use of paper and the cheapest price and category. In production and commercial trade, it is the reality that according to different use requirements, people will make various inspection standards for pulp quality, such as pulp whiteness, filtration, screening components, resin and ash content, cellulose content, hardness (On behalf of lignin content), physical strength of the pulp and other performance indicators of finished product. These standards refer actually to concrete reflection of fiber morphology and pulp purity. Paper production can choose one suitable category of pulp, or choose two or more different quality pulps by appropriate proportions.
Papermaking Processes
Papermaking processes consist of the following major procedures:
- 1. Pulping section: paper pulp raw material selection→ cooking for fiber separation→ washing →bleaching→ screening→ concentration and production for pulp chips→ storage
- 2. Papermaking section: pulp scattering→ impurity removal →pulp refining→ pulp beating → preparation of various additives → mixing of paper materials →convey of paper materials → head box → mesh section → press section → dry section → surface sizing → drying → calender →paper reeling
- 3. Coating section: raw paper coating→ coating → drying → reeling → re-reeling → super calendar.
- 4. Processing section: rewinding → cutting plate (or reel) → sorting and packaging → storage