Pulp bleaching is an important process in the pulp and paper industry. Its purpose is to improve the whiteness and whiteness stability of the pulp. This is achieved mainly through the role of chemicals to remove the lignin in the pulp or change the structure of the lignin chromophore. The traditional bleaching agents mainly include chlorine and hypochlorite and others. However, since 1980, the discovery that chlorine-containing bleaching agents such as chlorine and hypochlorite contained toxic organic chlorides just like dioxins that may have strong carcinogenicity has attracted widespread attention and promoted the improvements of traditional chlorine bleaching technology. The technology improvements and the development and application of oxygen-free (Oxygen, hydrogen peroxide, ozone, etc.) and pollution-free bleaching agents and bio-bleaching technologies are in bloom.
In recent years, with the enhancement of people's awareness of environmental protection, the pulp bleaching processing has achieved rapid development mainly to ensure the quality of the bleached pulp, while save energy and reduce pollution.
The Improvements of Traditional Chlorine Bleaching Process
The improvements of the chlorination process and equipment
The chlorination section as the first bleaching section in the multi-stage bleaching is very important. The chlorination section can selectively remove the residual lignin in the pulp and increase its bleachability. Chlorine is cheap and easy to be used, but its current chlorination equipment has the disadvantages of low chlorination concentration, long chlorination time, poor homogeneity and a large amount of waste water. Especially after dioxins are found in chlorinated waste water. The existing chlorination process and paper pulp making machines are accelerated.
How to reduce the amount of dioxins in waste water? It is currently considered to actively adopt the following measures:
- A. Change the current pulping and pulp bleaching process, including deepening delignification during the cooking process, providing low hardness unbleached pulp to thereby reduce the amount of chlorine used for chlorination: or introducing oxygen bleaching prior to the chlorination section to make the pulp hardness get reduced by half to make the amount of chlorine used in the chlorination section reduced. This can reduce the generation source of chlorophenols TCDD by 50%. The pulp washing is enhanced, and the amount of dissolved lignin in the black liquor is reduced to enter the bleaching process, thereby reducing chlorine consumption. In addition, the enhancement of the washing between C and E stages, the chlorine gas can be added by multiple times during the chlorination and the PH value is increased during the chlorination. These are all contributed to the reduction of toxicity in the chlorination and alkali treatment of waste water, particularly in the chlorination process. The method of adding chlorine oxide is commonly used to reduce the toxicity of bleaching waste water.
- B. Actively promote the use of chlorine-free bleaching or oxygen bleaching, such as oxygen bleaching, hydrogen peroxide bleaching, and ozone bleaching. They are the most basic methods for eliminating dioxins.
- C. Add a small amount of H2O2 during the bleaching of hypochlorite, reducing the production of trichloromethane and organic combined chlorine.
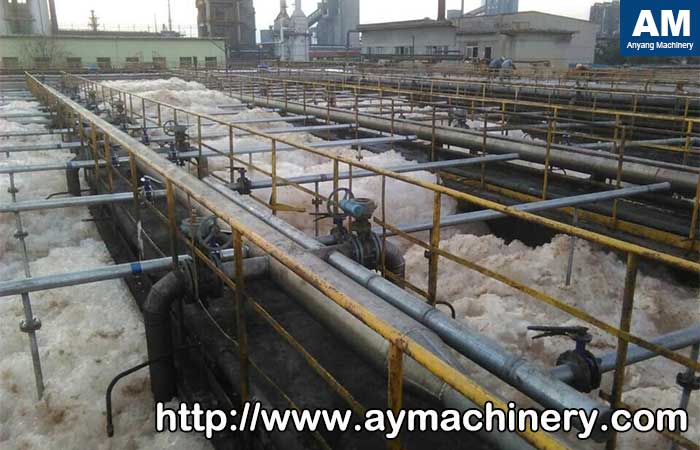
Development of chlorine dioxide bleaching technology
Chlorine dioxide is a selective bleaching agent. While it has a strong dissolving effect on the lignin in the pulp, it rarely damages the carbohydrates and affects the strength of the pulp. Chlorine dioxide is also a highly efficient bleaching agent. High levels of whiteness can be obtained with a small amount. The new development of chlorine dioxide bleaching technology is mainly in two aspects: one is the manufacturing method and the other is chlorine dioxide used in the chlorination section.
The rapid development of oxygen bleaching
The chlorine-free and multi-stage bleaching consisting of oxygen-containing bleaches, oxygen, hydrogen peroxide, and ozone do not contain toxic chlorides in the pulp and waste water while achieving high whiteness. And the waste water can be smoothly passed through the alkali recovery system. With the recovery of heat energy, the prospects are very good. It is also beneficial to use oxygenated bleaching agents instead of some chlorine bleaching agents in traditional multi-stage bleaching.
Oxygen bleaching and oxygen in the alkali treatment process
The oxygen bleaching has achieved rapid development in recent years. In high, medium and low concentration oxygen bleaching, it is believed that the use of 10%-14% of medium concentration oxygen bleach has good selectivity for delignification, saving chemical and energy consumption, and reducing water pollution. The waste water can be directly recovered. The bleaching pulp has high cleanliness, good whiteness stability, easy beating and low capital investment. At the same time, the oxygen bleaching also has a poor selectivity, that is, when it is bleached, it reacts with lignin and degrades carbohydrates, resulting in a decrease in pulp yield and strength. In view of the fact that the oxygen delignification capacity is not strong and its selectivity is poor, the oxygen delignification is generally controlled at a 40%-50% residual lignin removal to ensure pulp strength and yield (to be further improved the rate of lignin removal will inevitably cause a large amount of carbohydrates to be degraded, and the degree of fiber-fiber polymerization loss will be just over 20%). Therefore, adding appropriate additives to improve the reaction capacity of residual lignin and protecting carbohydrates is the key to the successful development and promotion of the oxygen bleaching technology.
H2O2 high concentration bleaching
As a non-polluting excellent bleaching agent, hydrogen peroxide is also a kind of delignification agent. Its application in bleaching chemical pulp includes three aspects:
- a. For the final stage of the multi-stage bleaching, the purpose is to further improve the stability of whiteness and whiteness stability and reduce chlorine consumption.
- b. For the medium stage for the multi-stage bleaching, it can replace H stage and E stage.
- c. For the first stage of the multi-stage bleaching, the purpose is to play the role of the delignification.
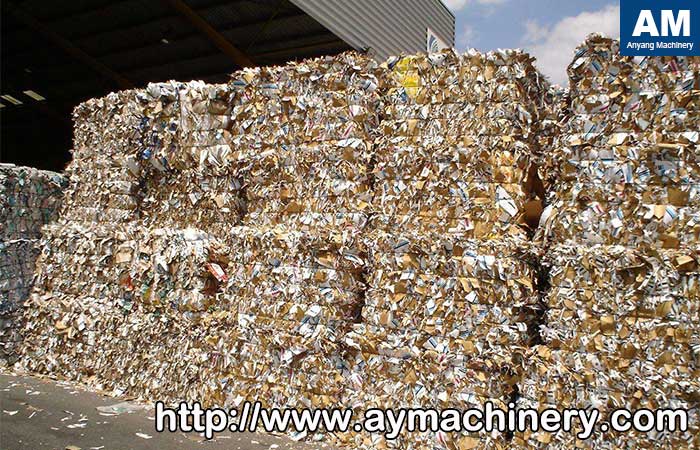
The ozone bleaching
Ozone is a light blue gas and a very effective oxidizing bleaching agent. It is suitable for the bleaching of various paper pulps. It has the characteristics of low bleaching temperature, short time, high bleaching efficiency, non-chlorinated waste water and easy treatment. In China and foreign countries, it has been doing many years of experimental researches. Franklin paper mill from American Union Compos Company had the production of 10,00tons per day of kraft pulp with the ozone bleaching process in 1992, creating a new era of a large-scale use of the ozone bleaching industry.
The diversity and flexibility of the pulp bleaching processing
In Europe, with the development of the pulp bleaching technology and paper and pulp technology, the bleaching process is no longer standardized just like that 10 years ago. But the bleaching process has diversified. Multiple and/or multiple-time additions of the bleaching chemicals may be used in the same bleaching stage.
From a long-term point of view, the chlorine-free bleaching has become the mainstream of the development of the pulp bleaching technology. This development trend will have an impact on the world's pulp and paper industry sooner or later.